Advancing Smart Meter Design: From FPGA to ASIC
A case study of Nano Genius Technologies
Smart meters are fundamental in today’s energy management because sustainability and efficiency define the success of a utility. Measuring energy usage is not just about using these devices; it is also about real-time communication regarding efficient energy distribution and cost savings. As the demand for smart meters grows, manufacturers are facing great challenges in scaling the designs for mass production.
This case study explores the strategic transition from FPGA(Field-Programmable Gate Array)-based smart meter designs to ASIC(Application-Specific Integrated Circuit)-based solutions. It covers the benefits of this transition, ASIC design flow, the problem of PCB design and manufacturing in India, and insights based on actual case study examples and trends in the industry.
The Problem: Limitations of Designs Based on FPGA
When developing and prototyping smart meters, FPGAs are a popular option. They are perfect for iterative design upgrades due to their adaptability and re-programmability. However, they are less feasible for large-scale manufacture due to a number of issues:
Exorbitant Production Costs: Although FPGAs are inexpensive to produce in small quantities, their cost per unit does not drop dramatically as production volume increases. When hundreds of thousands of devices are being produced, this becomes a serious problem.
Energy Inefficiency: Because FPGAs often use more power than ASICs, they are not appropriate for applications like smart meters, which must run constantly for years while using very little energy.
Design Constraints: FPGAs are general-purpose by nature. They are therefore unable to attain the same degree of optimization as ASICs designed for certain uses.
Consider Company X, a mid-sized urban smart meter manufacturer. There was a prototype that satisfied all their functional requirements but proved too challenging to produce in volume. Thus, it became increasingly expensive with inefficient power use and uncompetitive in the market.
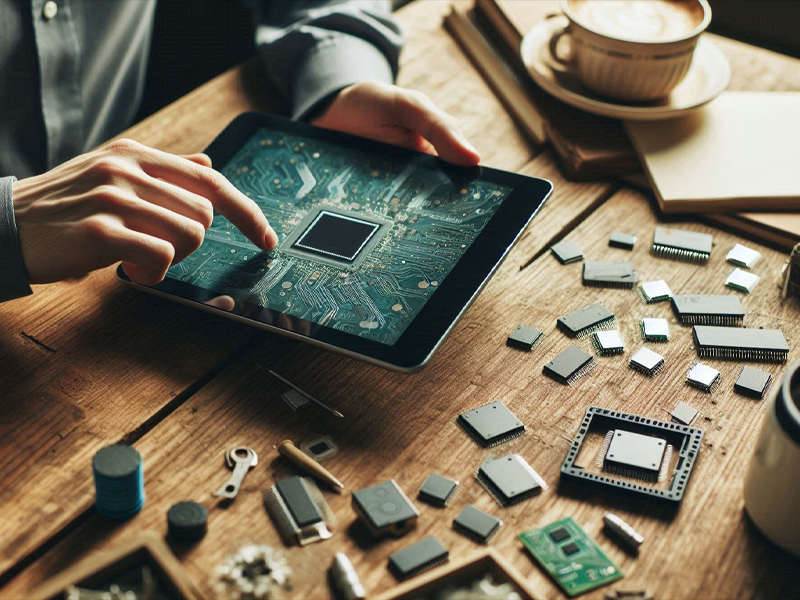
The Solution: Transitioning to ASICs
Switching to ASIC-based designs has several advantages, such as:
Cost-effectiveness: Because ASICs are made for specialized applications, they can be mass-produced for a fraction of the price of FPGAs.
Power Optimization: ASICs are designed for applications that need less power since they use less power.
Compact and Reliable Designs: ASICs make it possible to combine several functions onto a single chip. By doing this, the final PCB’s complexity and cost are eliminated.
For example, Company Y is the world’s leading company for smart metering technology. It reports reductions of 40% in production costs and 30% in energy efficiency after turning from FPGAs to ASICs.
ASIC Design Flow
FPGA to ASIC migration implies a structured methodology known as ASIC design flow. The ASIC design flow includes numerous phases:
Specification and Architecture Design: The process starts with defining the system’s functional and performance requirements. For smart meters, this includes:
Support for communication protocols like Zigbee, LoRa, or Bluetooth Low Energy (BLE).
High accuracy in analog-to-digital conversion for precise energy usage measurement.
Engineers develop a block-level architecture to address these requirements, specifying how various components will interact.
RTL Design and Simulation: Now, the RTL description will be written down in languages like Verilog or VHDL. This RTL code is the circuit’s functional behaviour. The correctness of the design will then be verified by employing simulation tools such as ModelSim or QuestaSim upon writing.
Synthesis: The RTL code is converted to a gate-level netlist using tools from Synopsys Design Compiler to optimize it for area, power, and timing constraints.
Design Verification: Verification verifies that the design meets the desired specifications. Techniques such as STA and formal verification bring out potential problems at an earlier stage.
Place and Route (P&R): P&R is the other part of the ASIC design flow. It is the placement of synthesized design components on the chip and routing connections amongst those components. Tools include Cadence Innovus, and Synopsys IC Compiler, which optimize for area, power, and performance during P&R.
Tape-Out and Fabrication: The design is then shipped out for fabrication to a semiconductor foundry once its correctness has been verified. The leaders here are the foundries, namely TSMC, GlobalFoundries, and SMIC.
Testing and Validation: After fabrication, the ASIC is subjected to thorough testing for all functional and performance requirements.
For a guide on ASIC design, click ASIC Design Flow Overview.
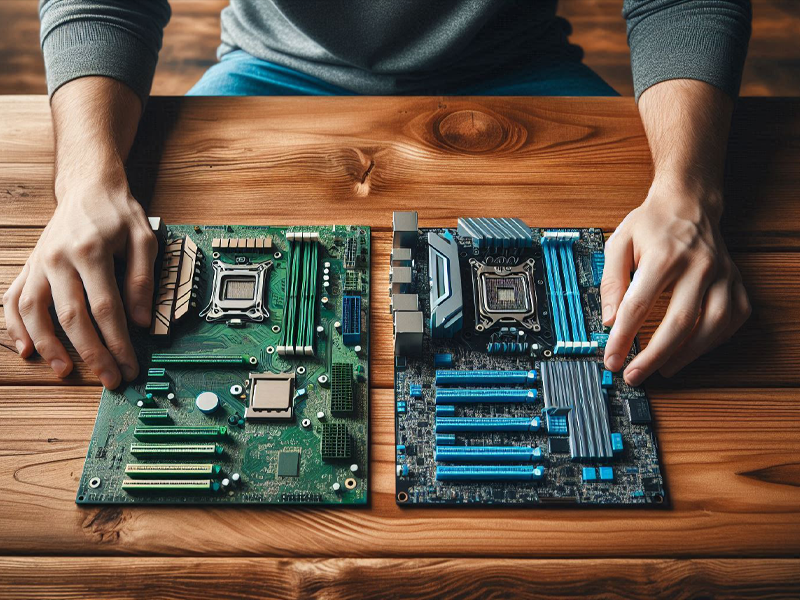
Challenges in PCB Design and Manufacturing in India
Even with the full functionality of an ASIC, transitioning from design to deployment requires including the ASIC in a PCB. This step introduces some unique challenges:
1. Thermal Management: ASICs are efficient but produce heat. Enhanced thermal management in terms of heat sinks and thermal vias shall be implemented.
2. Signal Integrity: Signal integrity is essential for high-frequency designs, particularly when integrating communication modules.
3. Manufacturing Infrastructure: Increasingly, the Indian PCB manufacturing environment, though growing, is however at low quality and uncompetitive prices.
Local manufacturers are responding to this by encouraging the demand from at least the PCB Power Market, Sierra Circuits, and AT&S India. The Production Linked Incentive (PLI) scheme put forward by the Indian government has also further increased the local manufacturing setup.
You can find more information about the setup of PCB manufacturing in India at PCB Power Market.
Case in Focus: Nano Genius Technologies
Nano Genius Technologies is one of the emerging IoT solution providers that managed to move their FPGA-based smart meters to ASIC.
Immediate Challenges
The FPGA-based prototype was powerful but expensive and power-hungry. Scaling up this for urban deployments was not feasible.
The Transition
Nano Genius teamed up with local PCB manufacturers in Bangalore, integrating their ASIC into a compact multi-layer PCB. They improved upon their design to support BLE communication, reducing power consumption by a large 35%.
Outcomes:
Cost Savings: This reduced the production costs by 40%.
Improved Reliability: The ASIC design enhanced device stability, reducing field failures by 25%.
Market Success: Over 100,000 units were deployed in Tier-1 cities, significantly boosting revenue.
Advantages of the Transition from FPGA to ASIC
The change produces several benefits:
Economic Scalability: Mass production is made possible by ASICs at a reduced cost per unit.
Enhanced Efficiency: ASICs perform better than FPGAs in terms of power and processing efficiency when tailored for particular workloads.
Localized Manufacturing: Lead times and imports were decreased by collaborating with Indian PCB producers.
Future Trends
Smart meters will have to incorporate newer features with advancements in technologies like 5G, AI, and IoT. Emerging trends include:
On-Chip AI Processing: ASICs that contain AI engines for analytics of the data.
Integration with Smart Grids: Increased connectivity for dynamic management of energy.
Frequently Asked Questions (FAQs)
Why is the transition from FPGA to ASIC cost-effective?
ASICs are tailored for particular applications, which ensure mass production at lower per-unit costs compared with FPGAs.
What are the issues in ASIC design?
The primary challenges are timing closure, thermal management, and regulatory compliance.
What is the support of PCB manufacturing for ASIC designs by India?
The PLI scheme of India and local manufacturers such as PCB Power Market offer affordable and reliable solutions that support ASIC-based designs well.
This case study underscores the transformative potential of transitioning from FPGA to ASIC in smart meter design. For more such insights, visit Nano Genius Technologies Case Studies.