What Every PCB Librarian Should Know About PCB Fabrication
Printed circuit boards are the backbone of almost all the devices, from a simple gadget to complex aerospace equipment, in the electronics world. One of the key functions in the PCB design process is the function of the PCB librarian. They have to create, manage, and maintain the component libraries upon which designers draw. Therefore, for the PCB librarian to ensure their libraries will result in designs that are efficient and manufacturable, they must understand the basics of PCB fabrication. Here is what every PCB librarian needs to know about this complicated process.
1. Understanding PCB Stack-Up and Layer Count
The PCB stack-up is the combination of conductive and insulating layers used to build a PCB. It has both top and bottom layers, with one or more intermediate layers according to the complexity level of the board. From electrical performance to manufacturability, everything depends upon the selection of the stack-up.
Why It Matters: Some parts are used in only specific layer counts or types of stack-ups. Knowing how stack-up impacts component choice helps the librarian avoid suggesting parts that will be impossible to make.
Action Item: Collaborate with fabrication teams to understand the stack-up restrictions, which include spacing and via requirements, reflected in a component footprint.
2. Standard Fabrication Tolerances
The acceptable variation in manufacturing dimensions, including trace width, spacing, and via size, are called tolerances. The tolerance depends on the capability of the fabricator; therefore, it is considered during the design of the library components.
Why it matters: If the footprints of the components included in the library exceed the tolerance limits, then this could lead to production errors or even failure to meet the design specifications.
Action Item: Each library component shall be made to meet the tolerance requirements of the capabilities of the PCB fabricator. Library footprints are updated based on the tolerance standards of the time.

3. Copper weight and trace widths
This value is expressed in ounces per square foot and relates the thickness of copper layers of a PCB. That leads to trace width requirements, the ability of carrying a current, and the strength of the board.
Why is it important? The overheating or even a total board failure can result in case the pad or trace width of a library component cannot support the expected current.
Action Item: Outline trace width recommendations in the component library by copper weight. Any components intended to serve as power or high-current components shall meet this requirement.
4. Clearance and Spacing Rules
PCB fabrication provides a set of strict rules for spacing traces, pads, and other conductive features so that they would not interfere with each other. Clearances are therefore determined by the board voltage level, component density, and the minimum spacing capacity of the fabricator.
Why It Matters: Erroneous clearances result in electrical shorts, signal interference, or even catastrophic failures at operation.
Action Item: Establish spacing parameters for library components consistent with minimum clearance specifications as required by the fabrication process. Coordinate with design teams to ensure the applicability of these rules.
5. Drill and Via Specifications
It makes holes for vias and for component leads. All fabricators have different capabilities on drill-and-via sizes. For instance, a kind of via: through-hole, blind, or buried is an element that could potentially impact manufacturability or cost on the board.
Why it Matters: Incorrectly sized vias—too large or too small—cause issues in the manufacturing process, weak solder joints, or unreliable connections.
Action Item: Include through recommendations within component footprints that reflect the drill capabilities of the fabricator and ensure that specifications meet the industry standards for reliability.
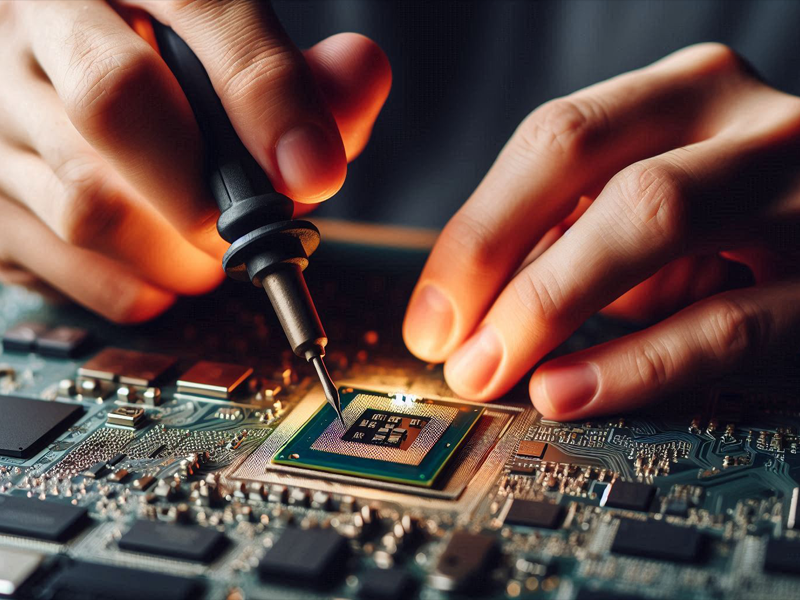
6. Material Considerations: FR4, Rogers, and Beyond
While FR4 is generic, board materials can range from high-frequency ones such as Rogers. Each material has specific electrical, thermal, and mechanical properties.
Why It Matters: Components with requirements for high-temperature applications or certain dielectric properties must match the board’s material.
Action Item Identify materials in the library as needed and collate by engineers’ selection of those materials.
7. Surface Finish Compatibility
Surface finishes like ENIG, HASL, and OSP affect solderability, placement of components, and long-term reliability. The benefits of different finishes are varying with different applications; librarians need to know which finishes are supported by the components.
Why It Matters Some parts require a specific finish to provide for adequate solderability or long-term reliability. A poor finish will produce a poor solder joint or corrosion.
Action Item: Add compatible surface finishes to the component specifications so that the designer will naturally choose parts that match up with the board’s intended surface finish.
8. Understanding the Role of DFM (Design for Manufacturability)
DFM rules are such that the PCB can always be made reliably and cost-effectively. DFM covers everything from how close components should be to the selection of standardized parts.
Why It Matters: A library component that fails to meet DFM rules may cause delays in manufacturing, higher expenses, or even rework of a design.
Action Item: Learn about DFM best practices and apply them to your library components—thus, avoiding exotic parts that are difficult to source or assemble.
9. Panelization and Component Placement
Panelization is an important planning step in which a set of several PCBs is assembled on a single panel, optimized for the efficient manufacture of the panels. Knowing beforehand where components are to be placed and how they will align and fit in the panels is therefore essential to avoid problems associated with overhang or difficult routing paths.
Why It Matters: Component placement directly influences the efficiency of panelization and impacts yield and manufacturing cost.
Action Item: Provide guidelines in the library as to where to place components and extend this to some high-density designs. Work with designers to layout for panelization requirements.
Conclusion
Beyond putting together, the right, true component libraries, the job of a PCB librarian addresses the details of knowing what it takes to create manufacturable design support. To accomplish this, by considering some of these fabrication principles, it makes sure that PC board librarians ensure seamless transitions from designs to production, cost-effective reductions, and enhanced products to depend on. The essentials to ensuring a rich and effective library are teaming up with fabrication teams and keeping aware of industry trends.
As PCB fabrication is intricate, a qualified and aware librarian of PCB can become vital in the production process for its successful completion.
Vendors, for more blogs and case studies, visit us at Nanogenius Technologies.